- Transformer Aluminium Strip
- Color Coated Aluminium Strip
- Aluminium Jacketing Insulation Coil
- PCB Entry Aluminium Board Strip
- Aluminum Plastic Composite Strip
- Aluminium Slit Strip
- Window Shutter Aluminium Strip
- Aluminium Corner Strip
- Aluminium Air Duct Strip
- Car License Aluminium Strip
- Heat Exchange Aluminium Strip
NEWS
INFORMATIONTel:
86 17344894490 Location : Home/Specification/ Production Process
Production Process
Last Updated :2023/07/04
Production Process
1. Melting and Holding Furnaces
![]() |
![]() |
Pure aluminium ingots are melted and alloyed with other elements by means of master alloy such as iron, silicon, manganese and magnesium. The material is analysed and adjusted to ensure the correct composition is achieved, then degassed, filtered and transfered to casting blocks to form aluminium slabs. The slab ends would then be sawn and scalped on both sides by slab saw. |
2. Hot Rolling Mesta 1+2 Stands Tandem Mill
![]() |
![]() |
![]() |
![]() |
The scalped slab is then placed inside the preheating furnace to be preheated / homogenized and made ready for the hot rolling process. The heated slab is hot rolled back and forward several times through the hot resersing mill to achieve a certain thickness prior to roll in the 1+2 Stand Tandem Mill.The finished products are hot rolled coils and plate materials for further process. |
3. Cold Rolling Davy Machine
![]() |
Hot rolled coils are then processed in the Cold Rolling Machine to customers' required Thicknesses and further treated in the annealing furnaces to achieve the required temper / strength. The Cold Rolling Mill machine is equipped with Automatic Gauge Control (AGC) and Automatic Flatness Control (AFC) able to produce the closest tolerances required meeting the stringent worldwide standards. |
4. On line Quenching
![]() |
![]() |
Hot rolled coils are then processed in the Cold Rolling Machine to customers' required Thicknesses and further treated in the annealing furnaces to achieve the required temper / strength. The Cold Rolling Mill machine is equipped with Automatic Gauge Control (AGC) and Automatic Flatness Control (AFC) able to produce the closest tolerances required meeting the stringent worldwide standards. |
5. Straightening Machine
![]() |
![]() |
Cold Rolled Coil are processed in the Finishing Department for further process as per customers' requirement such as :
- Tension Leveling for improving the flatness of the material prior to cut to lenght Line for final sheet products.
- Side Trimming for foil stock, slit coil and circle blanks.
- Embossing for embossed coils or sheets and roll forming for roofing products.
|
6. Strenching Machine
![]() |
![]() |
Aluminum foil is placed in the Annealing Furnace by means of heat treatment to reach a specific temper and mechanical properties required by customers. |
7. Polishing and Film Covered Procedure
![]() |
![]() |
The finished aluminium plates only have Mill Finish Surface,therefore,the polished surface need be produced as
customer’s requiremend.These plates will be put on transmission shaft firstly,then,they will be sent to the polished machine to get polished.
And the filim coverage machine joined with polished machine together in the end side.So as the film coverage will be done in the same time after plate polishing.
|
---> Punch to Aluminum Circle
![]() |
![]() |
![]() |
![]() |
Hot rolled quality or cold rolled quality of aluminum strip will be sent by conveyor to the Punching machine which gets punching head with different mold to produce various kinds diameter discs as customer’s requirement. |
Cut to Length ---> Aluminium Coil Strip
![]() |
![]() |
Cold Rolled Coil are processed in the Finishing Department for further process as per customers' requirement such as :
- Tension Leveling for improving the flatness of the material prior to cut to lenght Line for final sheet products.
- Side Trimming for foil stock, slit coil and circle blanks.
- Embossing for embossed coils or sheets and roll forming for roofing products.
---> Color Coated Aluminium Coil
![]() |
![]() |
![]() |
![]() |
Paint is applied using rolls. All paint systems are geared to match the requirements of the application. There are two primary types of coating: decorative and functional. |
---> Stucco Aluminium Coil Sheet Embossing Process
|
![]() |
---> Aluminium Tread Diamond Plate Process
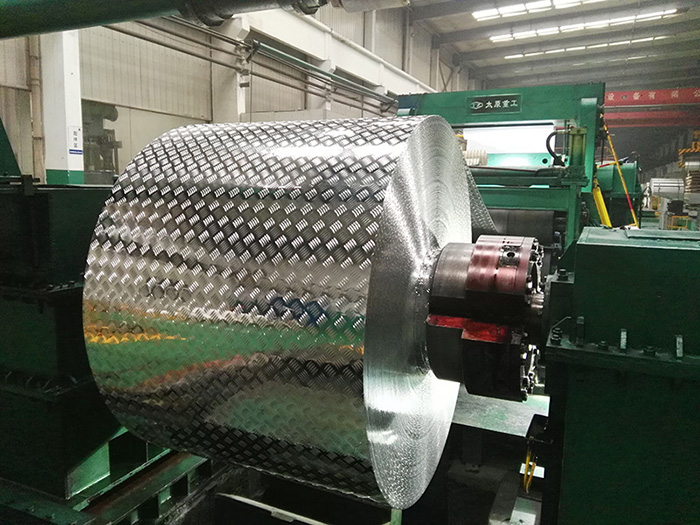
---> Mirror Aluminium Sheet
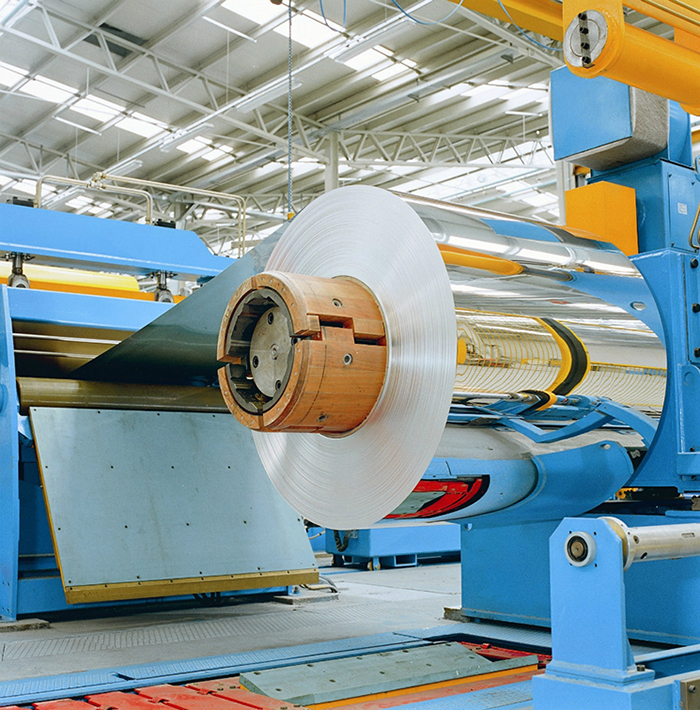
---> Aluminium Block
![]() |
![]() |
![]() |
![]() |